process









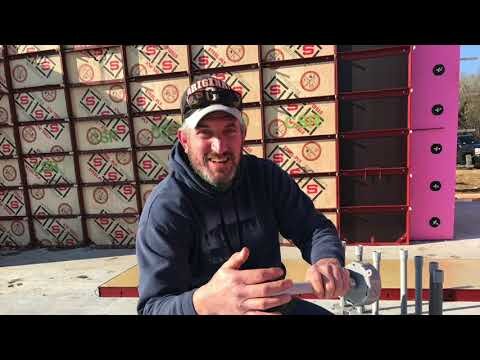



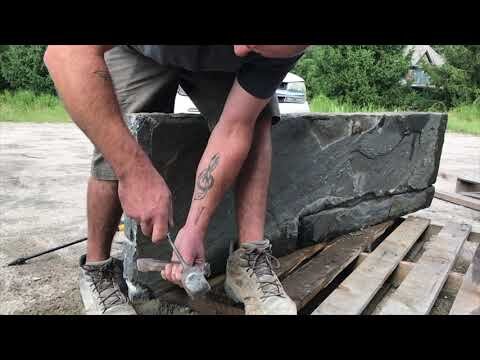
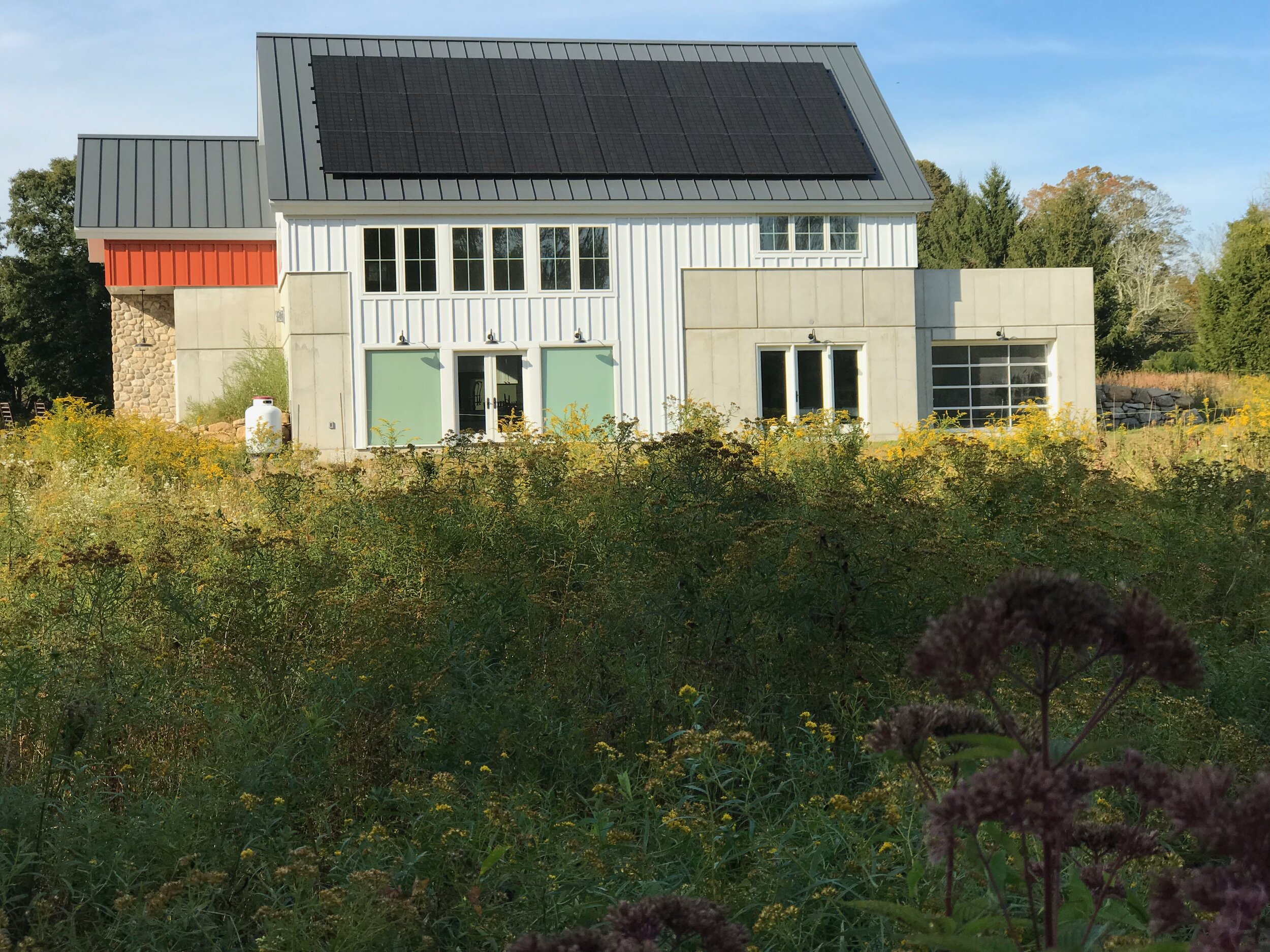
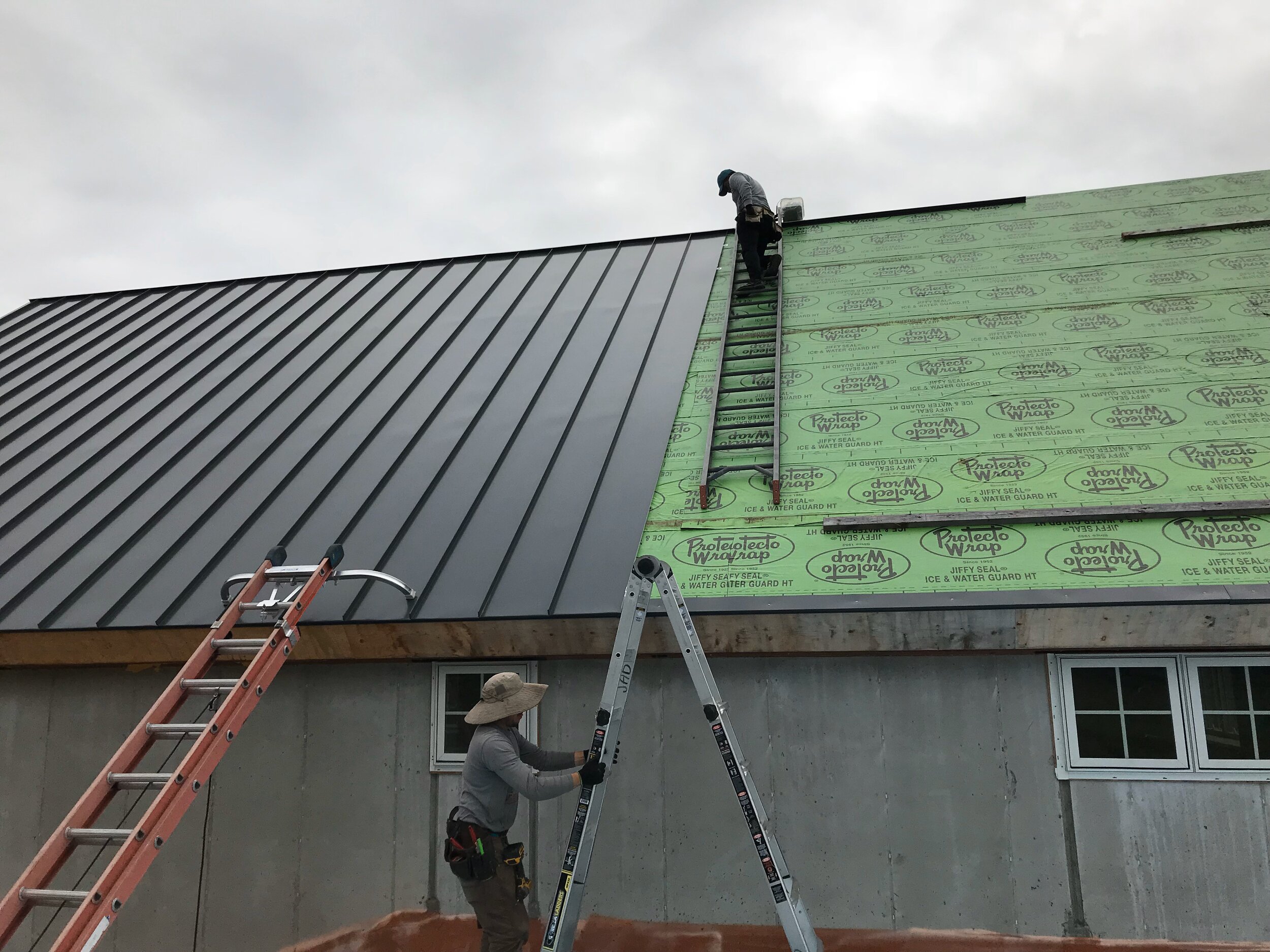
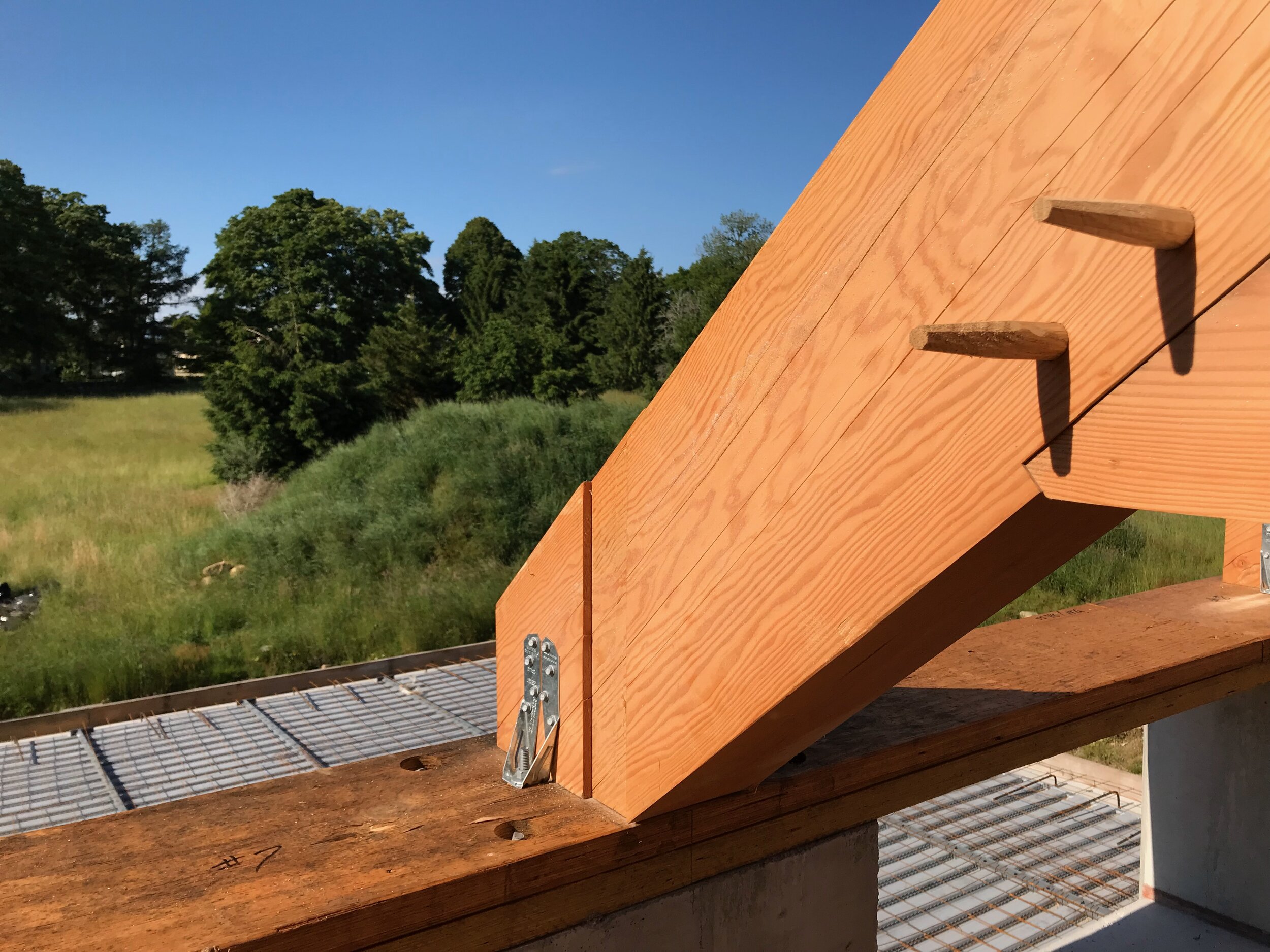
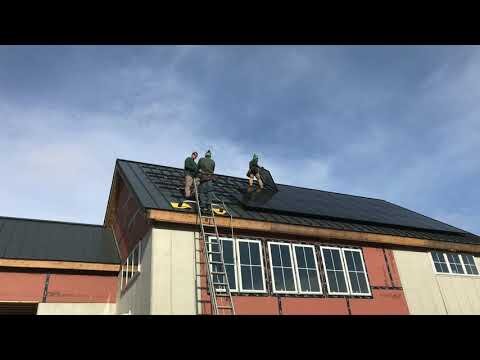
Pete O'Keefe of O’Keefe Construction breaks first ground. The topsoil is stockpiled on site and goes into the green roofs and berms next spring.
John O'Keefe and Dennis Purinton get down on the plans. 80% of this slab on grade house is Thermomass concrete, and there is no room for error.
Mike Purinton calls in the mixer to pour the Thermomass frost walls. 4” XPS foam insulation mates with the sub slab XPS for complete thermal break
Drone's eye view of the foundation, with plumbing and electrical conduit in place. This photo was taken just four weeks after breaking ground.
Master Plumber Jeff Shaw, CM John O'Keefe, Lead Carpenter John Bates and Master Plumber Steve Osella work on the sub-slab utilities.
Hot and cold water PEX supply lines will run free inside flexible polyethylene pipe, which is encased in 4" foam sleeves under the slab insulation, and in rigid conduit through the slab. The large conduit under the elbows is an electrical/data trunk. Once buried in concrete, these utility lines can be upgraded without too much fuss in the future.
Dennis Purinton guides the fiber-reinforced pour from Tilcon. Four inches of concrete over four inches of XPS foam rest on three feet of compacted stone and vapor barrier. When finished, the entire first floor becomes a thermal sink, moderating indoor temperatures throughout the year.
The cured slab and utility stubs are ready to be wrapped up for the winter. Come spring we'll be ready to pour the walls.
Master Carpenter John Bates, CM John O'Keefe and Kris Carr of Carr Concrete double check plans before the walls go up.
Forming up for Thermomass (VIDEO)
Joists from CanAm Steel support the garage green roof. Metal decking, 4” of concrete, 2” XPS foam insulation, drainage mat, sand and soil will complete the structure. Fiberglas form ties for the walls haven’t been trimmed yet.
Gable ends are framed to match the main roof trusses, 3,500 lb Douglas Fir assemblies designed and cut by Vermont Timber Frames.
Structural Insulated Panels, also designed and made by Vermont Timber Frames, are cored with graphite-infused Neopor, creating a tight R54 roof.
VIDEO: Local stone gets some engineering to provide veneers and a hearth.
Terra Cotta and Regal White steel siding from Drexel Metals wrap the Pella Impervia windows and doors. The 10Kw LG solar array from Waldo Renewable is grid-tied and battery-ready.
Steel roof panels from Drexel Metals being installed By J. A. Deniger’s crew.
Each of the five massive roof trusses from Vermont Timber Frames weighs about 3,500 Lbs. Two runs of LVL header beam work as a sill plate to spread the load on the Thermomass walls. 14”x1” EPDM sill gasket assures air tightness.
VIDEO: Waldo Renewable installs a 10Kw LG array and SolarEdge Inverter system.